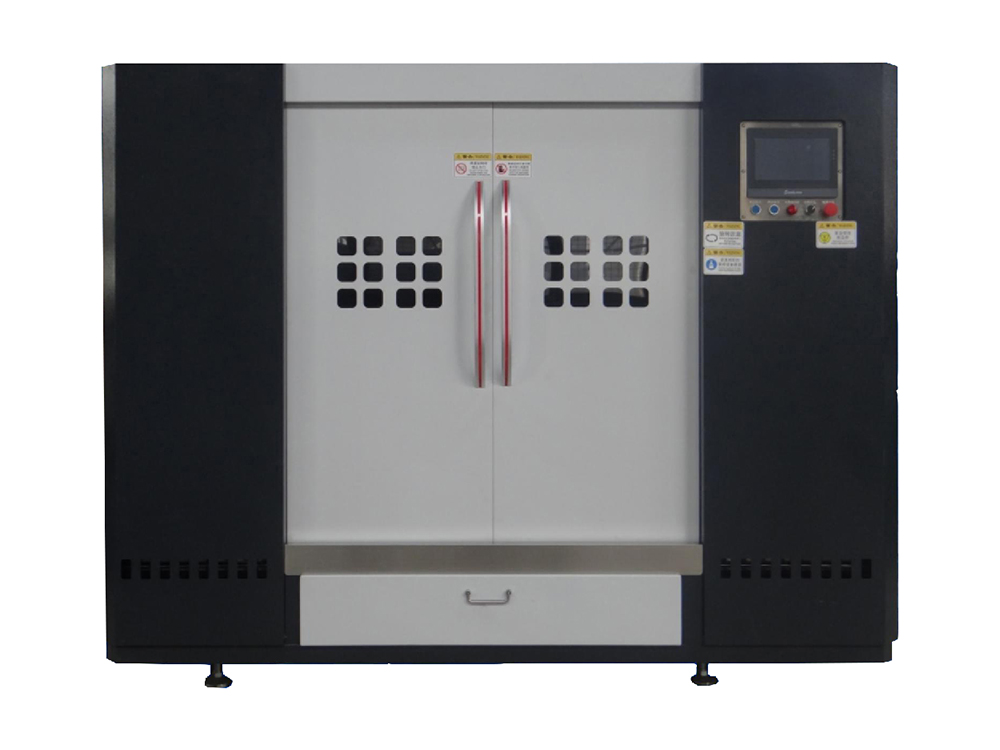
# Surface Treatment Equipment: Enhancing Material Performance and Durability
## Introduction to Surface Treatment Equipment
Surface treatment equipment plays a crucial role in modern manufacturing and material science. These specialized machines and systems are designed to modify the surface properties of materials without altering their bulk characteristics. From improving corrosion resistance to enhancing aesthetic appeal, surface treatment technologies have become indispensable across various industries.
## Types of Surface Treatment Equipment
Keyword: Surface treatment equipment
### 1. Electroplating Systems
Electroplating equipment uses electrical current to reduce dissolved metal cations so they form a coherent metal coating on an electrode. This process enhances corrosion resistance, wear resistance, and appearance of components.
### 2. Thermal Spraying Equipment
Thermal spray systems apply coatings by melting or heating materials and propelling them toward surfaces. These systems include:
– Flame spraying
– Plasma spraying
– High-velocity oxygen fuel (HVOF) spraying
### 3. Anodizing Equipment
Anodizing systems create protective oxide layers on metal surfaces, primarily aluminum. This electrochemical process improves corrosion resistance and allows for coloring of the surface.
### 4. Shot Blasting and Peening Machines
These machines propel abrasive media at high velocities to clean, strengthen (through peening), or prepare surfaces for subsequent treatments.
## Benefits of Surface Treatment
Surface treatment equipment provides numerous advantages:
• Extended component lifespan through improved wear resistance
• Enhanced corrosion protection in harsh environments
• Improved aesthetic qualities for consumer products
• Better adhesion for paints and coatings
• Increased surface hardness without compromising ductility
## Industry Applications
### Automotive Sector
Surface treatment is vital for:
– Engine components requiring wear resistance
– Body panels needing corrosion protection
– Decorative trim pieces
### Aerospace Industry
Critical applications include:
– Turbine blade coatings for thermal protection
– Corrosion-resistant treatments for airframe components
– Wear-resistant surfaces for landing gear
### Medical Devices
Surface treatments ensure:
– Biocompatibility of implants
– Sterilization capability
– Wear resistance for moving parts
## Emerging Technologies in Surface Treatment
Recent advancements include:
1. Nanocoatings
Ultra-thin coatings with exceptional properties at the nanoscale level.
2. Laser Surface Treatment
Precision surface modification using high-energy laser beams.
3. Environmentally Friendly Processes
New systems that reduce or eliminate hazardous chemicals and waste.
## Choosing the Right Surface Treatment Equipment
When selecting surface treatment equipment, consider:
• Material compatibility with the treatment process
• Required surface properties (hardness, roughness, etc.)
• Production volume and throughput requirements
• Environmental regulations and safety considerations
• Maintenance requirements and operational costs
## Conclusion
Surface treatment equipment continues to evolve, offering manufacturers increasingly sophisticated ways to enhance material performance. As industries demand higher quality, longer-lasting products with specialized surface properties, the importance of advanced surface treatment technologies will only grow. Investing in the right equipment and processes can provide significant competitive advantages in terms of product quality, durability, and performance.