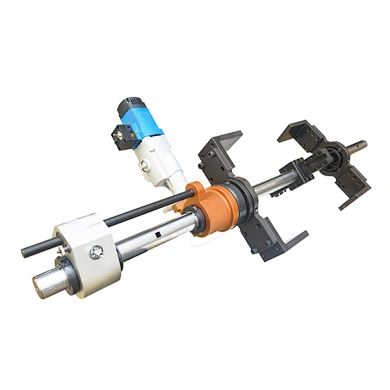
# Industrial Flange Facer: Essential Tool for Precision Machining
## Introduction to Industrial Flange Facers
Industrial flange facers are specialized machines designed to create perfectly flat and smooth surfaces on pipe flanges. These tools play a critical role in ensuring proper sealing and alignment in piping systems across various industries. From oil and gas to chemical processing plants, flange facers help maintain the integrity of critical connections that must withstand high pressures and temperatures.
## How Flange Facers Work
Keyword: Industrial flange facer
Flange facers operate by rotating a cutting tool against the face of a flange while maintaining precise alignment. The machine typically clamps onto the pipe or flange itself, allowing for on-site machining without the need to remove components from the pipeline. This capability makes them invaluable for maintenance and repair operations where disassembly would be costly or impractical.
### Key Components of a Flange Facer
– Cutting head with adjustable tooling
– Drive mechanism (often hydraulic or electric)
– Clamping system for secure attachment
– Alignment features for precision machining
– Chip containment system
## Applications Across Industries
Industrial flange facers find use in numerous sectors where piping integrity is crucial:
### Oil and Gas Industry
In refineries and offshore platforms, flange facers ensure proper sealing of high-pressure connections that handle volatile substances. Regular facing operations help prevent leaks that could lead to environmental hazards or safety incidents.
### Power Generation
Power plants rely on flange facers to maintain steam and coolant system connections. The precise surfaces created by these machines help prevent energy losses and maintain system efficiency.
### Chemical Processing
Chemical plants use flange facers to maintain connections that must resist corrosion while handling aggressive substances. Properly faced flanges reduce the risk of leaks that could lead to dangerous chemical exposures.
## Benefits of Using a Flange Facer
The advantages of incorporating flange facers into maintenance programs include:
– Reduced downtime by enabling in-place repairs
– Cost savings compared to flange replacement
– Improved safety through better sealing surfaces
– Extended equipment life by restoring damaged flanges
– Consistent results meeting industry standards
## Choosing the Right Flange Facer
When selecting a flange facer, consider these factors:
### Size and Capacity
Machines are available for various flange sizes, from small diameter pipes to large industrial connections. Ensure the model you choose can handle your specific requirements.
### Power Source
Options include electric, hydraulic, or pneumatic models. The choice depends on available power sources at your work sites and specific torque requirements.
### Portability
For field work, compact and lightweight designs offer advantages in maneuverability and setup time.
### Cutting Technology
Modern flange facers may use traditional cutting tools or advanced milling technology. Consider which approach best suits your material types and precision needs.
## Maintenance and Care
Proper maintenance ensures long service life and consistent performance:
– Regularly clean and lubricate moving parts
– Inspect cutting tools for wear and replace as needed
– Store in protective cases when not in use
– Follow manufacturer guidelines for specific maintenance intervals
– Keep electrical components dry and protected
## Future Trends in Flange Facing Technology
The industry continues to evolve with new developments:
– Automated alignment systems for increased precision
– Integration with digital measurement tools
– Lightweight composite materials for easier handling
– Smart sensors for real-time performance monitoring
– Environmentally friendly designs with reduced energy consumption
Industrial flange facers represent a critical investment for any operation relying on piping systems. By maintaining perfect sealing surfaces, these tools help prevent leaks, reduce maintenance costs, and ensure operational safety. As technology advances, flange facers continue to become more precise, efficient, and user-friendly, solidifying their position as essential equipment in precision machining applications.